pump casting foundry in china, there is much more to casting than selecting a process and making the appropriate pattern in pump casting process in china. During the past two decade since china entry into WTO. China pump castings suppliers manufacturers research and production experiences have provided scientific principles for better pump casting techniques.
For china pump casting foundry, the important considerations are the rate at which a pump casting mold cavity is filled, pump casting gate placement, pump casting riser design, the use of chill block of pump casting, and padding in pump casting process.
Filling the pump castings mold cavity. The velocity with which the molten metal fills the pump casting mold is determinded by the cross-sectional area of the gating system and mold-puring rate is the key factory for pump casting foundry foundrymanship.
Too slow a mold pouring rate means solidification before filling some parts of the mold. Allowing surface oxidation. Too high a pouring rate caused by too large gating system causes sand inclusion by erosion, particularly in green sand pump casting molding, and turbulence. These two all easy to cause pump casting defects
The minimum cross section in the gating system is called a choke. In the strict sense. The choke is the section in the gating system, when the gate system is choked at the bottom of the sprue.
It is called a nonpressurized system. This system is somewhat less reliable than a pressuried in which the choke is at the gate of pump casting molding system.
The first metal in the pouring basin and down the sprue usually has some turbulence that carries slag into the runner.To avoid slag in the pump castings, pump casting specialists suggested that the runner should extend past the last gate to trap the initial slag.
By the time the gates become operative. The liquid level should be high enough so that no slag can enter the pump casting cavity.
The runner should be laid out to minimize turbulence. That is it should be as straight and as smooth as possible. The gate is made to enter the cavity at the parting line of the pump casting mould.
pump casting specialists arrange gating may also be made at the top or bottom of the cavity. The parting lines gate is the easiest for the pump casting pattern maker to make;
However, the metal drops into the cavity, which may cause some erosion of the sand and some turbulence of the metal and finally cause for example like pump impeller casting defects
etc. For nonferrous metals, this drop aggravates the dross and entraps air in the metal of pump castings.
Top-gating is used for simple pump casting parts in gray iron, but not for nonferrous alloys pump casting materials, since excessive dross would be formed by the agitation.
Bottom gating provides a smooth flow of metal in the pump casting mold, however. If does have the disadvantage of an unfavorable temperature gradient. It cools as it rises, resulting in cold metal in the riser and hot metal at the gate.
Risers are designed by pump casting specialists and placed so as to ensure filling the cavity during solidification. They also act to relieve gas pressure in the pump casting mold and to reduce pressure on the lifting surface of the pump casting mold in china pump casting foundry
The volume of metal in the riser should be sufficient to retain heat long enough to feed the shrinkage cavity and to equalize the temperature in the pump body casting mold, avoiding casting strains.
The raiser requirements vary with the type of pump casting materials being poured. Gray cast iron pump casting parts, for example, needs less feeding than some alloys because a period of graphitization occurs during the final stages of solidification. Which cause an expansion that tends to counteract the metal shrinkage.
Many nonferrous metal pump casting part require elaborate feeding systems to obtain sound pump casting. The feed metal must be located above the highest point of the casting.
Chill Blocks are metal blocks placed in the pump body casting mold for localized heat dissipation. They may be placed at an intersection or joint where there is a comparatively large volume of metal to cool. thus relieving a hot spot or maintaining a more uniform cooling rate and better microstructure.
They may also be placed at the far surface of a pump body casting mold. Away from a riser or sprue. This will help the far end of the mold to freezed rapidly. Promoting directional solidification.
Chill blocks are also used by pump casting foundry at points where it is desirable to have localized hardening, as in the case of pump impeller casting process or pump bowl casting process.
Padding consists of adding to or building up a section to obtain adequate feeding of isolated section like some pump body casting and pump bowl casting, to feed central or outside boss of the pump body casting or pump bowl casting.
Can use risers with padding. Can provided a yield of say 45% of the metal poured. By the rule of thumb. The total thickness of pad and casting should not be less than one fifth of the metal feeding distance. This rule is not absolute but a good generalization in pump casting process.
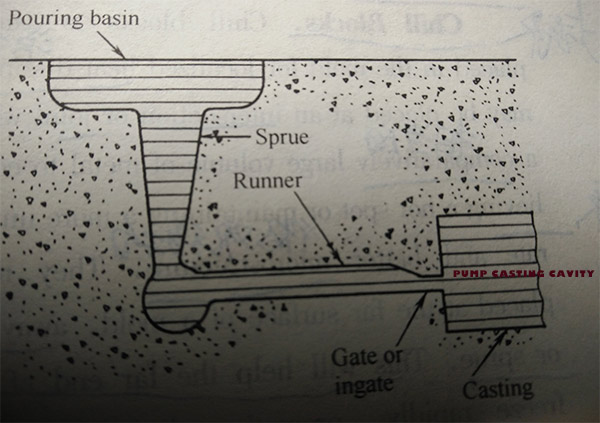
pump casting process
原创文章,转载请注明: 转载自DLFT CO.,LTD
本文链接地址: pump casting process used in china pump casting foundry